Waste in Lean: Eliminate Non Value-Adding Activities
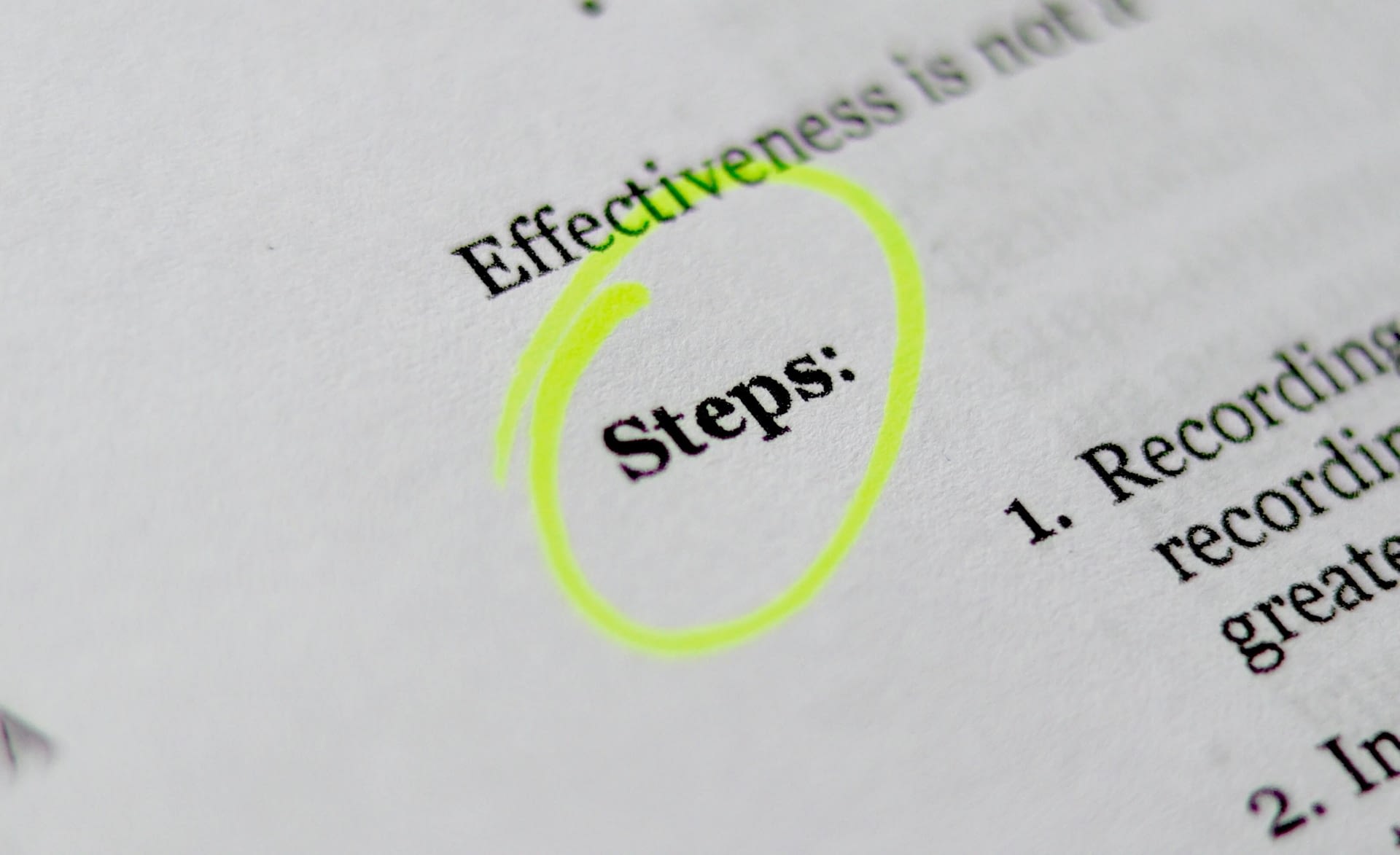
Waste in Lean falls under 8 defined categories. We discuss how to identify non value-adding activity in your processes from a Lean viewpoint and how doing so represents significant opportunity.
How much value adding activity is in your process?
Value adding means any activity that moves our product or service toward our customer at the right time, in the right quantity and to the customer’s expectation both internal and external.
When asked about value most process owners will initially believe that everything within the process is adding value. It all happens for a reason and it’s the way things need to be done. There isn’t anything inherently wrong with this. Most of the activity that happens is good and the process is working well. However with this mindset we can be accepting things that we shouldn’t. We can miss a great deal of opportunity for improvement.
In these situations improvement only comes in the guise of ‘bigger’, ‘better’, ‘faster’, and ‘more’. We ‘buy’ our way to improvement through spending and capital investment rather than innovating and challenging the status quo first.
The objective of any business process is to promote the unit of work to flow in the direction of the customer. That is, from order through to cash and to do so in the most efficient manner. Any process is composed of necessary and unnecessary activity. Necessary activity being value-adding and non-value-adding activities and unnecessary activity being waste.
The forms of waste in Lean
From a pure Lean viewpoint, waste (muda) is one of the three types of deviation that shows inefficient allocation of resources. The other two are unevenness (mura) and overburden (muri) – but more on these another day.
Waste in a process can take many forms. It is ultimately the inhibitor or disrupter of flow and causes much frustration and cost to all concerned. Typically, we may recognise waste as the physical items and scrap that goes in the rubbish bin. We also focus on the wasted time and effort of our people, or it can be the waste of doing things for no good reason at all. All of these things are relevant, however, from a Lean point of view we categorise waste in 8 ways.
A Lean approach essentially means we are trying to expose the waste in our process. Visually, we are aiming to eliminate the waste or at least improve the current situation with a clear problem-solving methodology. We are aiming to engage the key stakeholder in this process to find the single best way to deliver our service, or manufacture our product, in our process environment. This helps to provide a lexicon and a context from which to view waste from.
Waste isn’t always obvious
“How can there be so much waste?” You say. Well there certainly is; some of it obvious and some of it discreet. It all adds up to significant opportunity for improvement when we can expose it and remove it.
The priority is that we are focussed on the right waste – this is an important distinction. When we view Lean as a blanket elimination of waste we can spend a lot of time, energy and resources chasing shadows. This leads to working on things that will not have any great net effect on the process overall. We can actually sub-optimise the process by not considering the value stream as a whole. This is where having clarity and an understanding of how your value stream behaves, focussing on meaningful daily objectives and well considered strategic goals, comes into its own.
These standards and expectations simply serve the purpose of shining a light on where the obstacles are, how big they are, and generally help inform us on what to do next.
Categorising waste in Lean
The 8 wastes of Lean are as follows:
- Defects: Things that are not right
- Overproduction: Too much, too early, too fast
- Waiting: Not having what is required
- Non-use of skill: Not utilising the human potential in the organisation
- Transport: Moving things too far or too frequently
- Inventory: Too much stock, too little stock or having the wrong stock
- Motion: Excess human movement
- Extra Processing: Doing more than is required
When we are able to expose these process wastes on a daily basis we begin to paint a very clear picture of what is actually occurring in our process. We can compare this against what was assumed to be happening.
Very quickly we can see that not everything we do is adding value from the customers’ point of view. In fact, the reality is that only somewhere from 5 – 10% of the time taken to deliver the unit of work through the process is technically value-adding activity. The rest is non-value and waste.
This realisation is often a sobering moment, yet it opens our eyes to the scale of the opportunity to significantly improve our process and provide a superior customer service.
This is the reason why exposing waste quickly, simply and visually is the key to facilitating process improvement. It also enables engagement and learning to happen in real time. Developing the habits of daily waste reduction through problem solving and experimentation is fundamental to transformational change in your organisation. It will lead to a competitive advantage and the foundation for long term sustainable success.
Eliminating waste by removing 'locally optimised islands' from your greater C.I. Framework
Once we eliminate non value-adding activities from a Lean process we must ensure that they are supported by equally optimised adjacent processes and systems. Standardised problem solving techniques, Standard Operating Procedures and a Tiered Daily Management process that can handle the full PDCA loop helps to stop waste creeping in. These must not be optimised in isolation, but rather all developed in tandem to ensure we make the most from each process and avoid information silos.
This is exactly what we designed the TeamAssurance platform to achieve. The illustration below shows how we built an interconnected platform that avoids the locally optimised and disconnected ‘Point Solutions’ (digital or analog) that do not help and, in fact, hinder progress towards your goals.
TeamAssurance enables organisations to expose waste quickly and bake-in continuous improvement habits within all teams. If you would like to further explore Lean digital aids for your organisation (or your clients) contact us today for a platform demonstration.