Lean Innovation: Hybrid Digital Kamishibai Boards
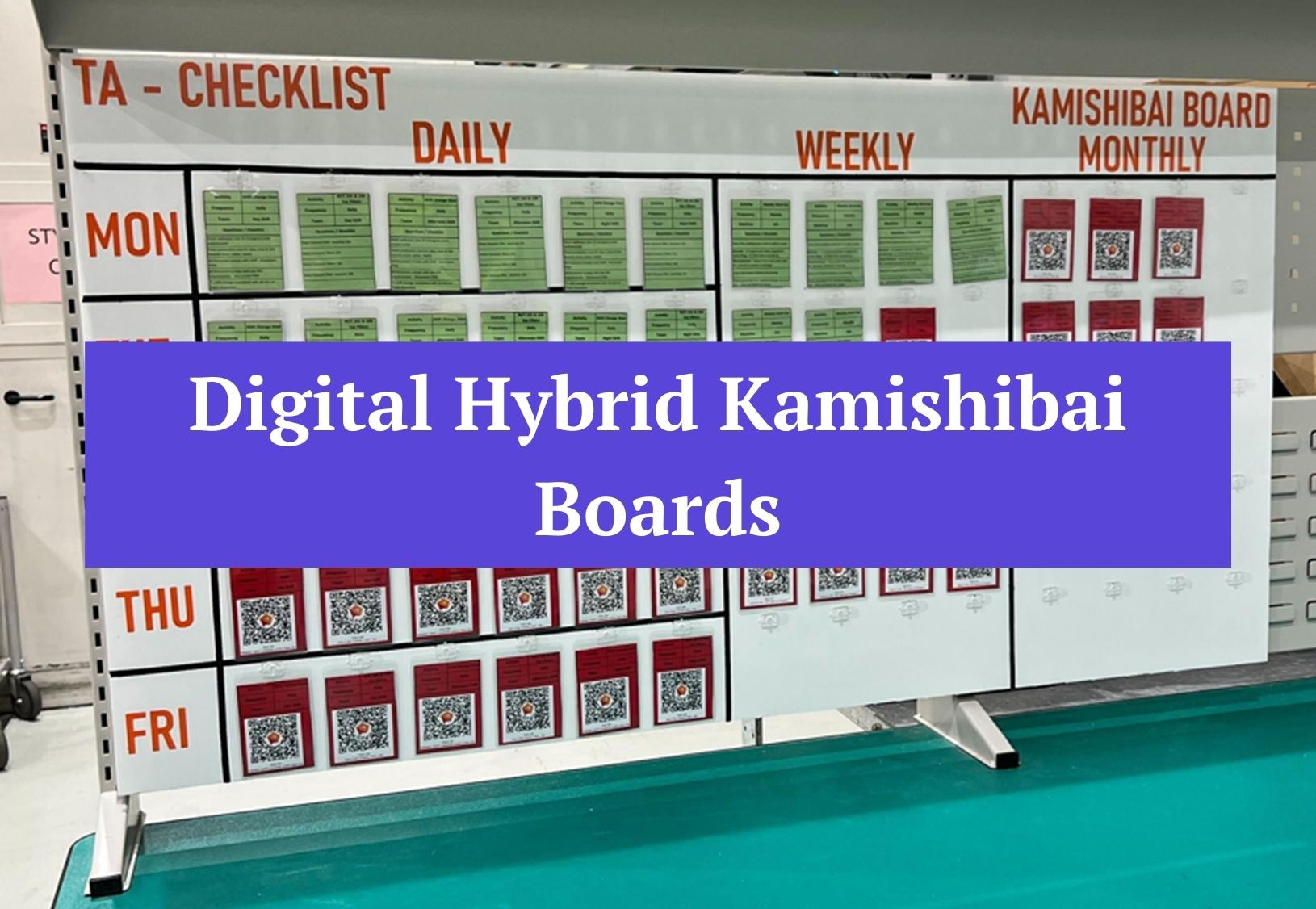
Digitising improvement doesn’t mean compromising on, or losing, your existing processes. Good digital aids to Lean tools should elevate and accelerate your existing processes - they are your hard won gains!
Recently, we visited an organisation who are doing just that with TeamAssurance; taking advantage of our QR Code Checklist functionality to digitise their Kamishibai Board.
What Is A Kamishibai Board?
Kamishibai Boards are a traditional Kaizen tool that enables organisations to standardise their audits and tell a story visually. They are a tried and tested tool for operators and leaders alike to conduct inspections at the Gemba in a uniform fashion.
The term Kamishibai refers to traditional Japanese paper theatre. This genre of storytelling is often centred around morality tales, allowing the audience to observe and compare their own experiences to that of the characters. A self-audit if you will. Hence, the Kamishibai Board - a board containing a set of standardised checklists for daily, weekly, monthly auditing.
A Hybrid Kamishibai Board in Action
In the video above you can see how both the physical Kamishibai board and TeamAssurance work together to enable staff to complete audits in a standardised manner, with more accuracy, greater speed, and at the Gemba.
By digitising the activities that the Kamishibai Board is visualising, the organisation is saving on waste and removing the barriers for staff to contribute easily & effectively.
The operator simply selects the required checklist tag from the physical board, scans with the phone camera, and follows the checklist prompts. Images can be taken and uploaded at the source, information saved to the cloud immediately and the audit completed much faster than traditional pen and paper methods.
Closing the Loop
When a frontline team member or a leader finds something that requires follow up, a task may be easily raised and assigned. This task flows in real-time, and allows people to act in real-time. These tasks then become an agenda item in each relevant function’s Tiered Daily Management meeting, allowing the team to discuss, prioritise, and surely follow up.
The trends seen in the follow up tasks (number, type) then become an agenda item in the leadership team’s Tiered Daily Management meeting, and so on. This closing of the loop makes certain that the next iteration of standard work is improved on, that employees have been heard, that trends of abnormalities have been identified - and that this routine work is truly meaningful and worth doing.
Removing barriers
'Frontline first' is a core TeamAssurance value. We exist to remove barriers to participation for this group because over the last decade they have become increasingly disconnected from the business information stack that is available to, well… everyone else.
Post pandemic, we can now safely categorise so much digital technology - cloud based applications, smartphones & tablets, and especially QR codes, as 'Household Technology'.
The example above shows an organisation that is recognising this, and moving in the direction of the Gemba, to make it easier for their frontline to engage & contribute, and not simply in the direction of what's easy for, well…‘everyone else’.
Part of a C.I. Framework, not a locally optimised ‘Island'
For a process to not only be sustained, but to thrive, it must be supported by adjacent processes. In this example, Leader Standard Work and autonomous maintenance must be supported by standardised problem solving techniques, and by Standard Operating Procedures.
These are delivered by a Training Management System and a Tiered Daily Management process that can handle the full PDCA loop to deliver the desired continuous improvement.
A schematic of the TeamAssurance platform below shows how we designed an interconnected platform which avoids the locally optimised and disconnected ‘Point Solutions’ (digital or analog) that do not help, and may even hinder your organisation’s main goal.
Want to explore the opportunities that digital-aids to Lean tools provide? If you’re a Business in need, or a Consultant with clients in need, contact us for a demonstration of the TeamAssurance platform today.